Running on efficiency at New Ventures
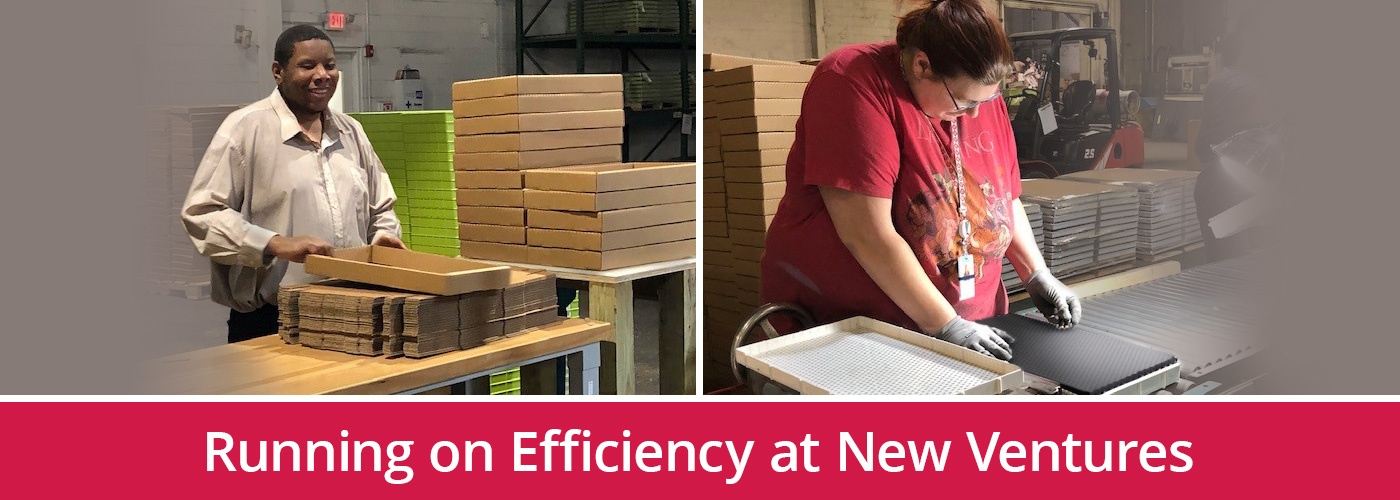
Going from two to 10 employees within a matter of months is a sign of success for any organization. Usually, this means that business is flourishing, and the customer is happy. For SourceAmerica member nonprofit agency New Ventures it means so much more than that. Welcoming eight new individuals to their Duracell contract means they have created meaningful job opportunities for professionals with disabilities in their community.
The process for this contract seemed straightforward to New Ventures -- receive the batteries, check them for quality, shift them from a plastic tray to a cardboard tray and then send them back for distribution. In total, they were loading just over 5 wooden pallets full of almost 230,000 batteries during some grueling weeks.
In January, the amount of batteries New Ventures received for processing increased significantly due to a change in their contract. Now they needed to load almost 100 wooden pallets full of nearly 3.6 million batteries a week. With this new workload in mind, the New Ventures leadership team reached out to a unique team of SourceAmerica engineers dedicated to working on solutions that increase productivity and efficiency for people with disabilities in the workplace.
Once the SourceAmerica productivity engineers arrived at the facility, they rolled up their sleeves to identify challenges and solutions that could be implemented to improve efficiency and ease pain points.
Challenge #1: Space for fulfillment of operation
With more work came the need for more room. The first thing the SourceAmerica productivity engineering team did was help New Ventures move their operation into a bigger space. That provided the opportunity to properly analyze and strategize on next steps.
With more space and a clear goal in mind, the team was able to triple their production lines (from one line to three), increasing efficiency for the entire operation.
Challenge #2: Battery tray efficiency
The batteries arrive at New Ventures in plastic trays with the negative end up. They are then reviewed for defects and flipped into another plastic tray with the positive end up. The battery positive ends are reviewed for defects and then the tray is flipped back again into a cardboard tray with the negative end up. Finally, the packaging material is added, and the trays are boxed and loaded onto wooden pallets for shipping.
If just reading the word flipped that many times had you confused, imagine the issues employees at New Ventures were having. Due to all the flipping, batteries would often come out of alignment in the trays and periodically fall to the floor. To prevent batteries from falling, the 34-pound trays had to be flipped manually by two employees on the team.
The productivity engineers saw an opportunity to modify the flipping tray for each new production line by cutting down the sides of the tray to fit the batteries more tightly. This enabled staff to replace the manual flipping with using a jig to flip the trays without any of the batteries falling out. This greatly reduced the fatigue employees were experiencing. In addition, spacers were added to make the trays snug, eliminating spills.
According to Mike L. Wilson, President and CEO of New Ventures, “With the help of the SourceAmerica productivity engineering team, we were able to streamline production lines. They really helped us reset the operation from the ground up.”
Results
The improvements alleviated many process pain points for New Venture employees. Professionals with disabilities working on this contract are happy, laughing and always doing their best. Their work is an important step in the distribution of this product.
To this day, the SourceAmerica productivity engineers continue to check-in with New Ventures to see how the new process is working and what modifications can be made. SourceAmerica and New Venture have indeed become valued partners.
To learn more about SourceAmerica contact customerservice@sourceamerica.org.
[PICTURED ABOVE (L-R): Cabriel Bruce forms the cardboard shipping trays. Cabriel is without vision, but does not let that keep him from being a very productive member of the New Ventures team; Emily Traylor inspects batteries on the AAA bulk line before packaging.]